近年来鹏飞集团对管磨机采用磨内筛分技术进行改造(亦称高产高细磨内改造技术)逐步受到业界人士的重视,主要是由于在这项改造技术中不需要增加设备和动力,只是对磨机内部结构进行改造,可以达到提高产量,降低电耗,提高成品比表面积的目的,加之投入少,技术改造时间短,所以很受欢迎。 采用磨内筛分技术对球磨机进行磨内改造的基本思路是:在普通管磨机内设置筛分装置取代原有的隔仓装置,运行中对前仓物料向后仓流动时进行强制筛分,拦截大颗粒,让这些大颗粒仍然回到前仓,继续用大尺寸的钢球进行破碎,合格的细料进入后仓。同时根据物料本身的特性、粒度、工艺状况,各仓配以合适球、段级配。这样前仓的料垫作用大大减弱,破碎能力增强,而细磨仓可采用大表面积的小规格研磨体,大大提高磨机的研磨能力,从而获得高产量、高比表面积的成品,最大限度提高磨机粉磨效率。 采用磨内筛分技术进行磨内改造实质是:强化了物料在磨内的分级功能。实现不同粒径的物料可以及时进入相应的粉磨仓中,从而可以使各种不同粒径的物料在最佳的粉磨机理的条件下完成粉磨作业,从而提高粉磨效率,降低能耗。 下面对采用磨内筛分技术进行磨机改造的相关技术进行详细的介绍和分析: 一、筛分装置 筛分装置是磨内筛分技术的核心装置,该装置性能的好坏是普通管磨机改造能否成功的前提。筛分装置性能优劣主要从这几个方面来考虑:一是筛分动力要大。由于该筛装置没有额外动力源,筛分过程的运动和动力是分别利用球磨机的自身旋转和被筛分物料自身的重力和侧压力来实现物料的筛分作业的。如何充分利用物料本身的重力和侧压力可以通过筛分结构的不同设计来调节,因此好的结构可以加强筛分动力,提高筛分效果。二是过料能力强,有好的筛分动力不一定过料能力就好,还必须有较大的筛分面积,使粗细料尽快筛分;三是通风能力强,最大限度改善磨内通风,降低磨内温度,防止磨内不良现象发生; 四是自洁能力强,消除筛分装置的堵塞现象;五是料位调节功能,可以使球仓保持最佳的料球比,以充分发挥球仓的粉碎效率;六是使用寿命长,这点往往在改造过程中被多数使用厂家所忽视。国内大部公司所采用的筛分装置大致分两类,一类是扬料板不带筛分板,使用寿命较长。但筛分功能由扇形筛分板完成,由于筛分动力为侧向堆积压力,筛分不彻底,筛分性能较差;另一类是扬料板带筛分板,筛分动力为重力,筛分彻底性能好,但磨损大、使用寿命短。由于中国制造能力的限制,筛分板一般用S=1mm不锈钢板或S=3mm冷轧钢板制作,寿命一般在6—8个月。 1.1、国内外现有筛分装置的结构 1)锥形筛板型筛分装置(1号) 该筛分装置由进料篦板和出料篦板、焊接在隔仓板架上的导料板、双向导料锥以及联接螺栓组成,结构如图1所示。 前仓内已磨好的物料通过进料篦板进入扬料板上,随着磨机的回转被提升导向,落到锥形筛板上,细料通过锥形筛板的筛缝落到卸料锥上,流入后仓。而未通过筛缝的粗料,只有沿着锥形筛板的表面流回一仓内重新粉磨。 2)微介质型筛分装置(2号) 丹麦史密斯公司制造的康必丹磨又称微介质磨,其适用的筛分装置又称微介质型筛分装置,结构如图2所示。 进料侧装有扇形的进料篦板,其后装有一层细筛板,隔仓板中心位置装有1个中心卸料锥,进料篦板与细筛板之间有一定的空间。支撑板为盲板,扇形出料篦板保护支撑板不被磨损。 当磨机工作时,前仓物料通过进料篦板的缝隙,进入和细筛板之间的空间,随着磨机的回转,细料穿过细筛板的筛缝落到扬料板上再被提升到上部,然后经过中心卸料锥的出料端泻落到后仓;而粗料和小研磨介质等也被类似于扬料板的小抄板带到高处,然后经过中心卸料锥返回到前仓,继续粉磨。 3)扇形筛板型筛分装置(3号) 合肥院推出的筛分装置,称其为内选粉筛分装置,其结构如图3所示。 其进料篦板的篦缝一般为同心圆环形或平行于弦长的直条形,篦缝较宽。紧贴进料篦板装有形状与其相同扇形筛板。出料篦板为盲板,或者带有辐射状的篦缝,缝宽尺寸较小。筛分装置与扬料板有分离组合型的,有组焊为整体的。 前仓物料在磨体回转作用下,进入进料篦板的宽篦缝内,小于扇形筛板筛缝的物料进入隔仓板内,在扬料板带动下,流向卸料锥的锥面泻入后仓。大于筛缝的物料,从进料篦板的篦缝返回前仓。 4)筛分仓型筛分装置(4号) 如图4所示,在扇形筛板型筛分装置的基础上,为了增加筛板过料面积,提高筛分能力,从结构上进行了改进,将筛板与进料端篦板拉开一定距离。在进料篦板与筛板间形成一个小空间,使粗细料在这个空间内进行筛分。笔者把它叫做筛分仓,把这种筛分装置称为筛分仓型筛分装置。 其筛分机理与扇形筛板型隔仓板基本相同,不同的是粗细料经进料篦板的宽篦缝进入筛分仓内进行筛分时,粗料不再从篦缝返回前仓,而是通过扬料板带动,流向卸料锥泻入前仓。由于筛板离开了进料篦板,被进料篦板篦筋所挡住的筛板筛缝也可发挥筛分能力。 1.2、国内外现有筛分装置的性能分析比较 1)筛分动力 以上几种筛分装置,物料进入和通过进料篦板的动力即物料侧向堆积压力和研磨体的冲击力,都是一样的。但物料通过筛板的动力却有所不同。对于3号而言,细物料通过筛板的动力与物料通过进料篦板的动力相同。对于4号而言,细物料通过筛板的动力只有物料的堆积力,并且由于筛分仓空间很小,物料也不会瞬时充满,所以物料的堆积压力作用也相对较弱。对于2号而言,细物料通过筛板的动力介于上述两者之间。对于1号而言,细物料通过筛板的动力则完全不同,细粉在重力作用下通过筛板,其动力是重力。 比较两种筛分动力,重力的筛分作用必然大于物料侧向堆积压力筛分的作用,其筛分效率也必然大于后者。不过由于筛分装置内空间有限,1号装置的筛板面积很小,总的过料能力还不如其它类型的筛分装置。 2)过料能力 筛分装置的过料能力主要取决于筛板上与物料接触的筛缝总面积和筛分动力。筛分动力相同,筛缝面积越大,过料能力越强;筛缝面积相同,重力筛分比侧向堆积压力筛分过料能力强。 1号筛分装置的筛板全部筛缝都与物料接触,但总面积过小,虽然重力筛分,筛分效率高,但总的过料能力弱。3号筛分装置筛板紧贴在进料篦板后面,约有一半的筛缝面积被篦板挡住了,过料能力降低。2号筛分装置过料空间较小,过料能力和3号近似。4号筛分装置筛板和进料篦板有一定的距离,全部筛缝均能发挥过料作用,过料能力是上述中最大的。 表1是以Φ2.2m磨机为例,各种筛分装置的过料面积, 类 型 筛分面积(mm2) 占截面比例(%) 筛分动力 锥形筛板型 84100 2.00 重力 微介质型 463020 9.70 侧向堆积压力 扇形筛板型 402050 9.12 侧向堆积压力 筛分仓型 1030300 23.20 侧向堆积压力 3)自洁能力 上述几种筛分装置中,进料篦板篦缝最大为20 mm,最小的只有12 mm。在磨机运行中,与篦缝尺寸相当的物料和破碎的研磨体,极易卡在篦缝内引起堵塞,减小篦缝面积,甚至达到70-80%的篦缝被堵塞,严重影响筛分装置的过料能力。物料或破碎的研磨体卡入篦缝后,能在其它物料或研磨体冲击下脱离篦缝,称为筛分装置的自洁能力。 2、3号筛分装置的筛板紧贴在篦板后面,进入篦缝内大于筛缝的物料必须沿篦缝返回或逸出。3号筛分装置中,尽管篦缝成倾斜状,以利于进入篦缝的大颗粒物料(含研磨体)在回转到筒体上部时在重力作用下从篦缝中脱落。但大于篦缝的物料或研磨体位于筒体下部时,在物料挤压或研磨体冲击作用下挤入篦缝后,没有一定的外力作用不易逸出,且会越卡越多,影响过料能力和通风,所以这两种筛分装置自洁能力较差。 1、4号筛分装置的筛板和篦板有一定距离,使篦缝完全形成通孔,卡入篦缝的物料或研磨体一般会在物料挤压或研磨体冲击下通过篦缝进入筛分仓内,在扬料板、卸料锥作用下返回前仓。所以这两种筛分装置自洁能力相对较强。 4)通风能力 早期的筛分装置出料端篦板为盲板结构,除了各篦板相邻处的装配间隙外,只有中心锥的通风板可以通风。如2、3号筛分装置通风能力很差。 1、4号筛分装置的出料篦板上设置了辐射状篦缝,但为了阻挡后仓研磨体进入筛分装置,一般篦缝宽度尺寸设计很小。后仓研磨体稍经磨损容易卡入篦缝内,减小篦板通风面积。 5)料位调节能力 上述四种筛分装置中,只2号筛分装置具有料位调节功能,其他都没有。 1.3、GA型筛分装置 盐城大志环保科技有限公司的AET研发中心利用日本独资企业的优势,根据中国管磨机的实际情况,吸收日本最先进的技术,运用大型计算机集成系统模拟磨机运行设计出适用于中国管磨机改造的高产高细磨内筛分改造技术以及GA系列筛分装置, 1)结构及筛分原理(如图5所示) 其进料篦板的篦缝一般为同心圆环形或平行于弦长的直条形,篦缝宽(一般大于最大的物料粒径)。紧贴进料篦板装上带有筛板的组合扬料板,筛板筛缝大小根据不同客户的具体情况确定,扬料板后面装有形状与进料篦板相同,带有一定筛缝的扇形筛板,筛缝大小根据不同客户的具体情况确定。出料篦板带有辐射状的篦缝,在扇形筛板后面,和扇形筛板之间有一定空间。主要支撑和保护扇形筛板。 前仓物料在磨体回转作用下,从进料篦板的宽篦缝进到扬料板上,扬料板带动粗细粉混合料沿筛分板流动,小于筛板筛缝的物料在重力作用下进入扬料板的细粉流动空间通过卸料锥细粉出口进入后仓,大于筛缝的物料,从卸料锥粗粉出口返回前仓,同时细粉还可以通过径向筛分板直接穿过出料篦板进入后仓。 2)性能 从筛分动力上讲,在扬料板上的筛分属于重力筛分,筛分效率特别高;在径向筛分板上筛分属于侧向堆积压力筛分。所以和上述四种筛分装置相比具有筛分动力大,筛分效率高的优势。 从过料能力上讲,GA筛分装置比上述四种筛分装置中过料能力最好的4号筛分仓型筛分装置的过料面积要多出45%左右,而且多出的部分其筛分动力为重力,试验证明其筛分效率是4号筛分仓型筛分装置3.4倍。 就自洁能力而言,GA筛分装置的进出料篦板采用大篦缝设计,篦缝宽度分别大于前后仓的最大物料粒径,物料可自由通过篦板进入筛分仓进行筛分,而不会堵塞篦缝,所以GA筛分装置的自洁能力是最好的。 从通风能力讲,GA筛分装置整个截面处于全贯通状态,通风阻力小,不堵塞,通风面积大,所以通风性能特别优良。 GA筛分装置可以根据用户需要进行前后仓的料位调节。 GA筛分装置和其他形式的筛分装置相比另一个优势在于使用寿命特别长,是一般筛分装置的3倍以上。GA筛分装置进、出料篦板采用中合金钢油淬火工艺,筛分板采用钼铬锰合金板加工,其他部分采用耐磨材料加工。 二、磨内结构及相关工艺参数的确定 有了好的筛分装置只是普通管磨机改造成筛分磨的一个基础,更重要的是磨内结构及相关工艺参数的确定,它直接决定了磨机改造的成败。为了科学地进行磨内改造,盐城大志环保科技有限公司AET(无锡)技术研发中心在深入的理论研究的基础上进行大量的试验、数据处理和经验总结,提出筛分磨工艺参数确定的科学理论和方法,并在实践中取得了良好的效果。 2.1、筛分循环负荷率和筛分效率 1)筛分循环负荷率 筛分循环负荷率是指筛分装置的返回前仓量F和通过筛分孔进入后仓的量G之比。 设:W---筛分装置喂入量,吨/小时; a---筛分装置喂入料细度(通过筛分装置筛孔的百分数); F---筛分装置返回前仓量,吨/小时; b---筛分装置返回前仓料细度(通过筛分装置筛孔的百分数); G---筛分装置进入后仓量,吨/小时; c---筛分装置进入后仓料细度(通过筛分装置筛孔的百分数);=1 L---筛分循环负荷率, 根据物料平衡得 W=F+G W.a=F.b+G.c 二式联立得 (F+G).a=F.b+G.c L=F/G=(c-a)/(a-b)=(1-a)/(a-b) 2)筛分效率 筛分效率是指筛分通过量与筛分装置喂入量中可以通过筛孔量之比.其计算公式如下: X=G/(F+G).a=〔(a-b)/a.(1-b)〕×100 式中 X---筛分效率,%。 筛分循环负荷率过低,前仓内物料流速慢,“料垫”作用大,不利于发挥筛分的产量高,电耗低的特点。 筛分循环负荷率过高,筛分效率低,易堵塞。不利于前仓的破碎,易发生饱磨等不良现象。因此合理的筛分循环负荷率对于管磨机磨内筛分改造很重要。 表2各种不同的管磨机粉磨系统进行磨内改造的筛分循环负荷率一般可考虑如下: 筛分循环负荷率(%)开流粉磨系统 圈流粉磨系统 一、二仓间 二、三仓间 一、二仓间 二、三仓间 锥形筛板型筛分装置 110~125 75~90 95~105 65~755 微介质型筛分装置 65~75 42~55 60~70 35~45 扇形筛板型筛分装置 65~75 42~55 60~70 35~45 筛分仓型筛分装置 50~62 35~42 42~50 30~38 GA型筛分装置 38~45 22~30 30~42 15~22 2.2、仓长 管磨机进行磨内筛分改造,确定仓长非常重要。仓太长,筛分循环负荷率过低,不利于发挥筛分的产量高,电耗低的特点。仓太短,筛分循环负荷率过高,筛分效率低,易堵塞,不利于前仓的破碎,易发生饱磨等不良现象。而且每个仓仓长确定的方式和侧重点是不一样的。 例如一个三仓管磨机进行磨内筛分改造,而且一、二仓之间和二、三仓之间都采用筛分装置。在进行改造前首先必须对该磨机的工艺状况有一个详细的了解,做一个筛余曲线,同时对磨机不同部位进行物料粒径分析。在确定一仓仓长的时主要考虑一仓的破碎效果。一般对于Φ2.6m以上的磨机的一仓仓长L和直径D比值L/D=0.95-1.05比较适宜,入磨物料粒度越小则越短。对于小于Φ2.6m的磨机的一仓仓长L和直径D比值L/D=1.1-1.25比较适宜,入磨物料粒度越小则越短。对于磨前有预粉磨的粉磨系统,则需要根据所筛分物料某一粒径的含量和筛分循环负荷率来确定。在确定二仓长度时,要根据一、二仓筛分装置的筛分粒径和二、三仓的筛分装置的筛分粒径及由表2确定一个适宜的筛分循环负荷率,运用磨机原来的筛余曲线进行确定。 对于二仓管磨机在确定一仓长度时主要根据入磨物料的粒径和一、二仓筛分装置的筛分粒径,由表2确定一个适宜的筛分循环负荷率,运用磨机原来的筛余曲线进行确定。 对于圈流粉磨系统的仓长的确定方法和开流系统类似,只是选择筛分循环负荷率不同而已。 2.3、筛分装置的筛径 筛分装置的筛径的确定主要由前仓长度、入磨物料的平均粒径、筛分循环负荷率和物料的水分和物料的种类等因素决定。 例如对于三仓水泥磨而言,一、二仓筛分装置的筛径可由改造前的筛余曲线、拟确定筛分装置部位的物料粒径分析和筛分循环负荷率来确定。二、三仓筛分装置的筛径则是由物料的易磨性、第三仓的长度和研磨体及级配、出磨物料的比表面积决定。主要考虑控制入第三仓物料的最大粒径,使得物料通过第三仓研磨后达到比表面积要求,同时又保证适宜的筛分循环负荷率。 圈流系统的筛分装置的筛径一般比开流系统的筛分装置的筛径要大;物料水分大,则筛分装置的筛径相对较大;筛分性能差的筛分装置的筛径要大。 生料磨一般不宜进行磨内筛分改造,特别是二、三仓之间一般不可采用筛分装置,主要原因是水分大筛孔容易堵塞。一、二仓如采用筛分装置,筛径一般不宜小。对于矿渣磨而言,由于矿渣本身易磨性差,不易堵塞。所以筛分装置的筛径可以取小一些,特别是筛分装置的筛径要通过试验确定,否则可能造成出磨矿渣粉比表面积达不到要求。 2.4、钢球、钢段级配 普通管磨机经过磨内筛分改造后,使物料在磨内各仓用相应尺寸的研磨体逐级粉磨,并及时逐级筛分。各个仓内的物料粒径组成发生了变化,同时物料流速加快,产量增加,因此各个仓的研磨体级配要作适当调整。 对于三仓磨而言,经过磨内筛分改造后,一仓内料垫作用减弱。主要目标是将入磨物料迅速地破碎到某一粒径(由筛分装置的筛径决定),因此在研磨体的级配上以二到三球级配较合适,可以去掉部分小球,充足部分大球。对于二仓而言,由于物料经过筛分,所以物料粒径很整齐,没有大粒径物料,粉料也会很快被筛分进入三仓。所以的研磨体中大的部分要剔除,采用适合的研磨体,级配以三级适宜,以较大研磨体为主;对于三仓而言,主要任务是将一定粒径的粗料一次性研磨成一定比表面积的成品,所以增加研磨能力是主要调整目的。一般采用中段或微段或小钢球,以二级级配为主。同时可以加装活化衬板以提高研磨能力。 当然,球段级配的调整是一个很复杂的过程,要根据各个水泥生产厂家的具体情况实施,不能一概而论。而且调整的幅度不宜过大。 三、性能及效果分析 4.1与普通高细磨和其他型式筛分磨相比 运用盐城大志环保科技有限公司的磨内筛分改造技术打造成的筛分磨与普通高细磨、其他型式筛分磨相比具有明显的优势,主要体现在以下几个方面: 1)普通高细磨的筛分腔窄,球仓的小钢球或破球以及块状物料很容易进入筛分腔而卡住,使立筛板变形或破损,影响筛分效率,而GA筛分装置不存在这种缺陷结构; 2)普通高细磨的筛分依赖于内置的“立筛板”,物料从前仓到后仓的流动完全依赖磨内物料料面差来完成,是一种侧向堆积压力作用的“静态”筛分;而GA筛分装置采用的是滚动筛,物料在滚动筛上运动的同时进行筛分,因此是一种重力作用的“动态”的筛分,筛分效率更高。 3)普通高细磨的筛分板是平面结构,很容易变形和破损,而GA筛分装置中用于筛分的滚动筛是立体结构,难于变形和损坏。 4) GA筛分装置的物料分选系统设计了径向立式筛板,取消了普通高细磨中的盲板,这一结构设计对解决长磨机粉磨过程中糊球、糊段、通风不良尤为有利。 4.2与闭路磨相比 运用磨内筛分改造技术打造成的筛分磨与普通高细磨、其他型式筛分磨相比。它的高效率主要来源于大比表面积的微锻和内置的物料筛分系统,综合两者的特点具有相得益彰的效果,它与传统的闭路磨相比有着不可争辩的优势,主要体现在以下几个方面: 1)投资方面 以φ2.2×7.5m磨机为例,闭路磨系统包括选粉机、提升机、回灰输送设备以及土建设施投资大约在50万元左右,而选择磨内筛分改造技术进行改造,仅需9万元左右(主要包括: GA筛分装置、GA活化装置、GA磨尾卸料装置)。新用户磨机本体部分外购,“内脏”由盐城大志环保科技有限公司配置。 2)磨机产量方面 普通闭路磨由于选粉机选出的粗粉进入球仓,对球的冲击形成缓冲效应,削弱了球的破碎能力,影响磨机产量的发挥。而磨内筛分改造技术打造成的筛分磨的破碎仓和研磨仓有着严格的分工。球仓主要“破”,锻仓主要“磨”。内置物料筛分系统,能及时将破碎仓的细粉选出并送入研磨仓,提高球仓及锻仓的破、磨效率。一般情况下,在同样比表面积条件下,对普通闭路磨运用磨内筛分改造技术改造,产量都有较大提高。 3)节约能耗方面 闭路磨的生产工艺相对复杂,需要一台选粉机和2~3台提升、输送设备,因此需提供大量的电能来支持这些设备的正常运行。运用磨内筛分改造技术打造筛分磨为开路生产,内置GA筛分装置随磨机筒体运转无须动力。以φ2.2×7.5m闭路磨为例,选粉机加上提升及输送设备总装机容量85kw左右,改造后每天节约电费800元,年费用25万元左右。 4)提高比表面多掺混合材方面 普通的闭路磨(指配转子式选粉机或离心选粉机)水泥比表面积在300㎡/㎏左右。而运用磨内筛分改造技术打造成的筛分磨的粉磨工艺为开流生产,加上微型钢锻的高效率研磨,水泥比表面积都可确保340㎡/㎏以上,水泥三天强度提高3~5Mpa,至少可多掺混合材5%左右,吨水泥生产成本下降5元左右。 5)改善水泥颗粒级配,提高水泥品质 水泥颗粒级配对水泥性能有直接的影响,特别是32um以下颗粒含量对强度增长起主要作用,而大于65um的水泥颗粒难于水化,活性很小最好没有。运用磨内筛分改造技术打造成的筛分磨可改善水泥颗粒级配,提高水泥品质。以φ2.2×7.5m闭路磨机为例,对改造前后的水泥产品分别取样,测试结果如下:改造前细度控制≤3%,产量在16.5t/h左右,32um以下水泥颗粒累积分布为54.93%,大于65um的水泥颗粒累积分布为21.98%;改造后为开路磨,在同样工况条件下细度控制≤4%,产量在17t/h左右,32um以下水泥颗粒累积分布为92.91%,大于65um的水泥颗粒为2.3%。水泥三天强度平均提高4.7Mpa。 6)物资消耗和设备运转率方面 由于闭路粉磨系统工艺相对复杂,设备增多,人力、物力、财力消耗在所难免。取消选粉机运用磨内筛分改造技术打造成的筛分磨为开流磨,简化了工艺流程,设备运转率大幅度提高。 7)研磨体消耗方面 由于锻仓主要以研磨为主,加之微锻选用优良材质,微锻的消耗相当低,约30克/吨水泥左右;微锻的冲击力小,因而锻仓衬板的磨损亦相应减小,钢球的消耗与普通磨机差不多。 8)劳动强度及劳动环境 取消选粉机开路生产,无粗粉回灰,磨头的回灰扬尘没有了,配料现场的工作环境得到了很大改善;再有进入锻仓的物料经过严格分选,磨尾的笼筛出口再也见不到粗颗粒的熟料和其它物料,劳动环境和劳动强度大为改观。 四、磨内改造过程中的注意事项 管磨机磨内改造中失败的案例较多,或者说双方合作满意的较少。主要是由于磨内筛分改造成是一项系统工程,全面掌握有很大难度。就我们调查后发现失败的原因大致有以下几个因素。 1、筛分装置的性能差,对整个磨内改造技术不完全掌握。只是更换筛分装置,没有对整个系统的工艺参数作适当调整,造成技改效果不明显,甚至出现负作用。 2、改造前双方交流缺失。业务人员为了做成业务,片面夸大磨内筛分改造的效果。结果改造后实际的效果和所说的效果相差过大,造成双方合作不愉快。实际上对于运行正常的管磨机进行磨内筛分改造产量提高一般在15-20%左右,降低电耗15%左右。 3、改造过程中双方配合不协调是失败的另一个很重要的原因。从事磨内筛分改造的公司掌握更多的是共性的东西,在改造过程中必须得到生产厂家的大力配合。 4、对开流系统和圈流系统的筛分改造是不同的。用开流系统的筛分技术对圈流系统改造是很难成功。 五、结束语 磨内筛分技术提高粉磨效率是不容置疑的。但正确使用要有一定科学性和系统的协调性,使用不当不仅不能起到提高效率的作用,反而会降低效率,甚至导致粉磨作业不能正常运行。磨内筛分技术的应用并不单纯是将原有的隔仓板更换成筛分装置,该项技术应该理解为粉磨系统技术。因此使用磨内筛分技术时应从如下几个方面来全面考虑:1、粉磨对象的各项属性、粉磨设备的规格的研究和把握;2、磨内筛分装置结构的选择和位置的确定;3、粉磨系统形式、设备的组成和各工艺参数的研究和确定。所以说这项技术是一个具有系统性特征的技术,而不是单纯的筛分装置技术。磨内筛分技术对于不同的用户、同一用户不同的粉磨系统的组成,所选用的结构和工艺参数是不相同的,必须针对每一个粉磨系统进行专门的研究和进行专项方案设计。这个方案设计不仅仅表现在项目实施的初期,更重要的是体现在现场的安装和调试的过程当中,也可以说这项技术是粉磨系统的现场调试技术。这项技术的使用对方案设计人员和现场安装和调试人员有着很高理论基础和实践经验的要求。一方面从理论上要求技术人员对筛分理论、磨内工艺参数研究、粉磨系统的组成、粉磨机理有比较深刻的研究和理解;另一方面要有丰富的实践经验、现场分析问题和现场决策的能力。应该说这才是这项技术价值的真正体现。
1629
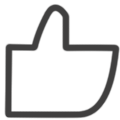
- 1苏州天启高速混合机手册
- 2纳米石墨烯电镜检测
- 3纳米石墨粉粒度检测(复达)25-0630
- 4电池材料表征实践指南
- 5聚合物加工测试分析指南
- 6散量秤彩页
- 7无斗定量包装秤—毛重秤彩页
- 8电子舌在牙膏质量控制和研发的应用
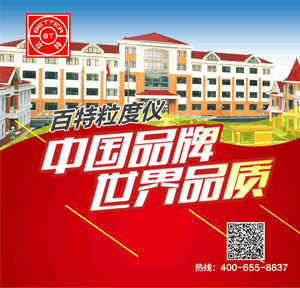
- 为什么AFM、NC等期刊频繁报道多孔水凝胶的最新研究进展?
- 蓝宝石的10大应用
- 《JMST》顶刊揭秘:激光3D打印高强铝合金的“强韧协同”奥秘——协同晶粒细化策略
- NC、AFM等期刊报道银纳米线最新研究进展!
- 为什么ZIF-67的最新研究进展值得关注?
- 经典介孔分子筛SBA-15又有新进展!
- 利用蜂鸟声共振技术对穿心莲内酯纳米混悬剂的开发、表征和分子动力学模拟
- 为什么核壳复合纳米材料的研究进展值得关注?
- Development, Characterization, and Molecular Dynamics Simulation of Andrographolide Nanosuspensions Utilizing Hummer Acoustic Resonance Technology
- 苏州碳丰科技首席科学家程金生老师以本公司名义在国际上发表关于石墨烯纤维的论文《石墨烯纤维纳米复合材料的合成及氨基酸检测的分析应用》:
- 介可视·散装物料库存管理雷达全景扫描系统在料仓、堆场中的应用
- 磷酸化修饰鬼臼果多糖的制备及生物活性
- DSR论文解读:Advanced Science News 报道中科院长春应化所新型非铂催化材料研究成果
- High-throughput preparation, scale up and solidification of andrographolide nanosuspension using hummer acoustic resonance technology(纳米混悬剂制备的前瞻性技术 - 蜂鸟声共振)
- 扫描电镜优秀论文赏析|飞纳台式扫描电镜电极材料上的应用
- 扫描电镜论文赏析-干旱影响杨树叶片及次生木质部发育的分子机制
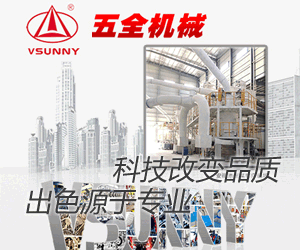